By clicking a retailer link you consent to third-party cookies that track your onward journey. This enables W? to receive an affiliate commission if you make a purchase, which supports our mission to be the UK's consumer champion.
Types of wood flooring
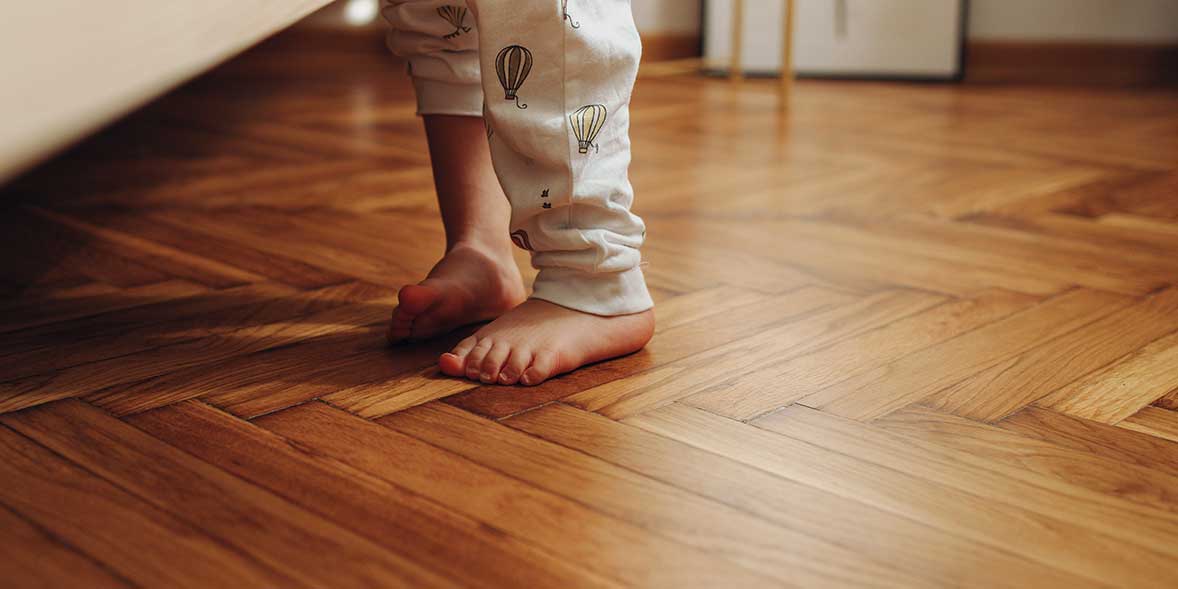
From modern laminate to reclaimed hardwood, wooden floors are a popular choice for homeowners.
Not only are they durable and easy to clean, they come in plenty of varieties to suit both contemporary and classic style rooms.
In our expert guide, we explain the pros and cons of different types of wood floor, the rooms to which they are best suited, and how much you can expect to pay.
Be inspired to make home improvements. Sign up for our Home newsletter – it's free monthly
Engineered wood flooring
Pros of engineered wood flooring
- Cheaper than solid wood
- More durable than solid wood
Cons of engineered wood flooring
- More expensive than laminate
- Sensitive to its environment – as well as warping in high humidity, it can fade in bright sunlight
- Can be fiddly to install
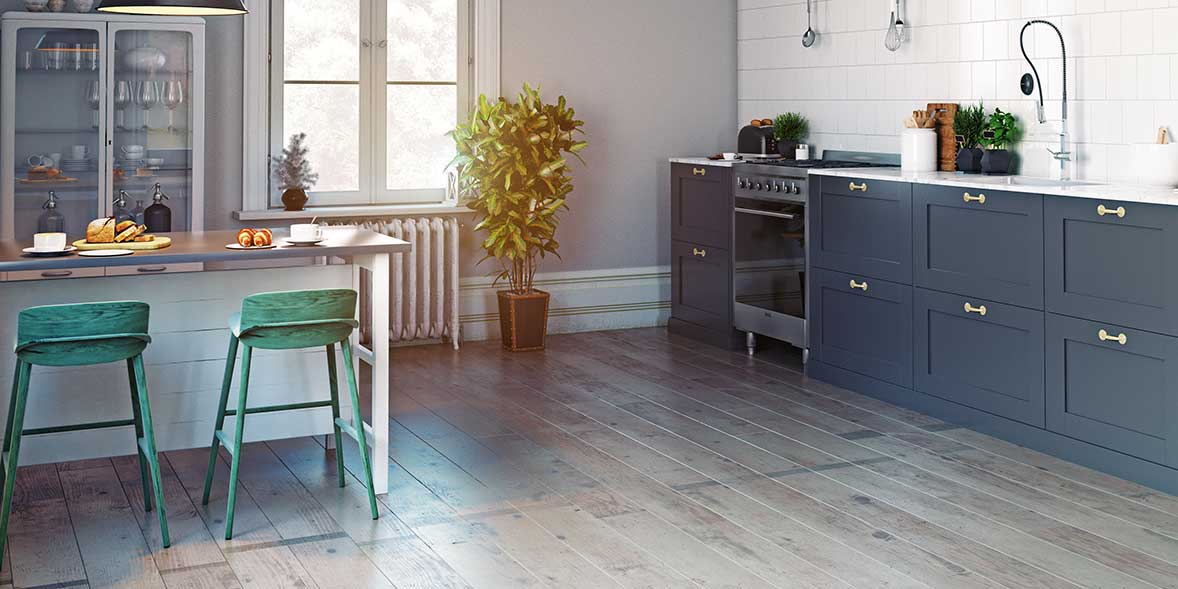
Engineered wood floorboards consist of three or four layers of wood, glued together to create a plank around 14mm thick.
They have a real-wood veneer of around 4mm thick on top (the wear layer), so that they can be sanded back and treated to restore the original finish if damaged.
Engineered wood flooring is sometimes available with click-lock installation, which doesn't require any adhesive.
Tongue-and-groove versions will need to be glued into place. Skip ahead to tongue-and-groove vs click-lock flooring for further advice on these two types of joint.
How much does engineered wood flooring cost?
Prices start at about £19 per square metre, but can be more than £160 for expensive woods.
Where to lay engineered wood flooring
The durability of engineered wood means that it's suitable for most living spaces, including living rooms, dining rooms, bedrooms and kitchens.
However, it's best avoided in rooms with high humidity, like bathrooms. While it's more resistant to warping than solid wood, it can still change shape over time.
Laminate flooring
Pros of laminate flooring
- Cheap and hard wearing
- Wide range of styles available
Cons of laminate flooring
- Less durable than a solid wood floor
- Doesn't feel like a wooden floor
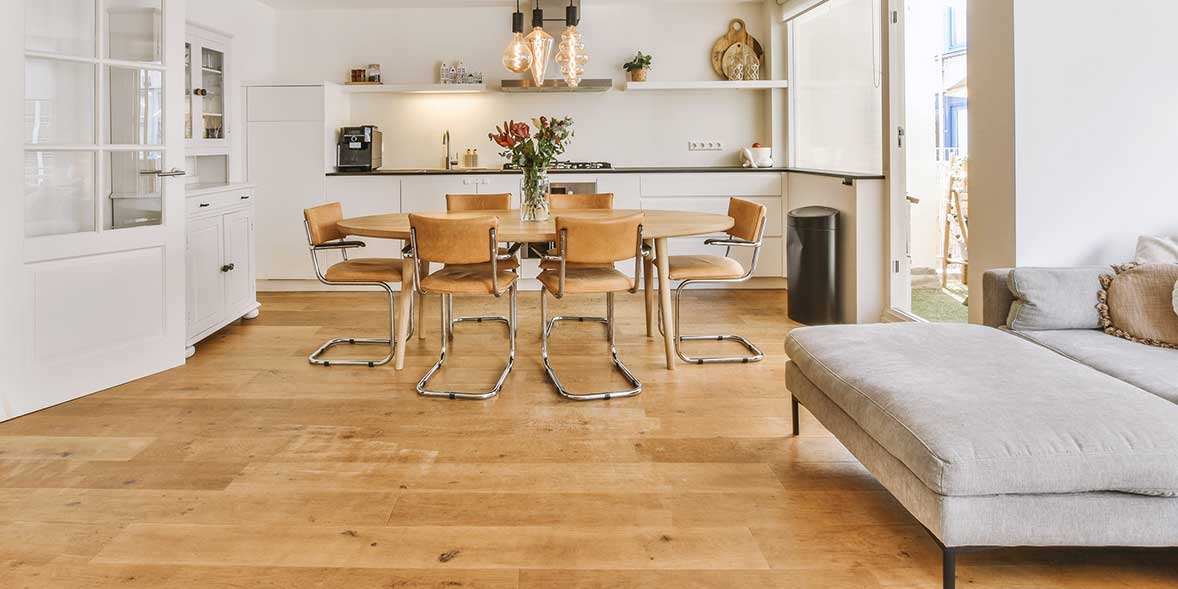
Laminate flooring is made of a compressed fibreboard plank, which is covered by a photographic image of wood and topped with a protective overlay.
The quality can vary considerably, so it pays to buy the best quality you can afford.
The edges of some laminate flooring boards have a slight bevel to create a more realistic appearance. It also helps to avoid damage caused by moisture-induced swelling at the edges of laminate boards.
Avoid laminate flooring with a chipboard core, because it expands and contracts a lot, and look for a fibreboard base with a plain-coloured underside (usually green or brown) for added protection against moisture.
How much does laminate flooring cost?
You can find some options for as little as £8 per square metre, but be aware that the cheapest types will not look realistic or be particularly durable.
Where to lay laminate flooring
Laminate is suited to high-traffic areas that need frequent cleaning, such as living rooms, studies and playrooms.
Some include a waterproof core, which manufacturers claim makes them suitable for bathrooms and kitchens.
If you're still considering different flooring types, read our guide to how to buy the best carpet
Solid wood flooring
Pros of solid wood flooring
- Has a classic look and feel
- Generally feels cooler in the summer and warmer in the winter
- A desirable feature for homebuyers, so it can increase your home's resale value
Cons of solid wood flooring
- Generally more expensive than other options
- Not very stable (swells in damp conditions)
- Tough to install
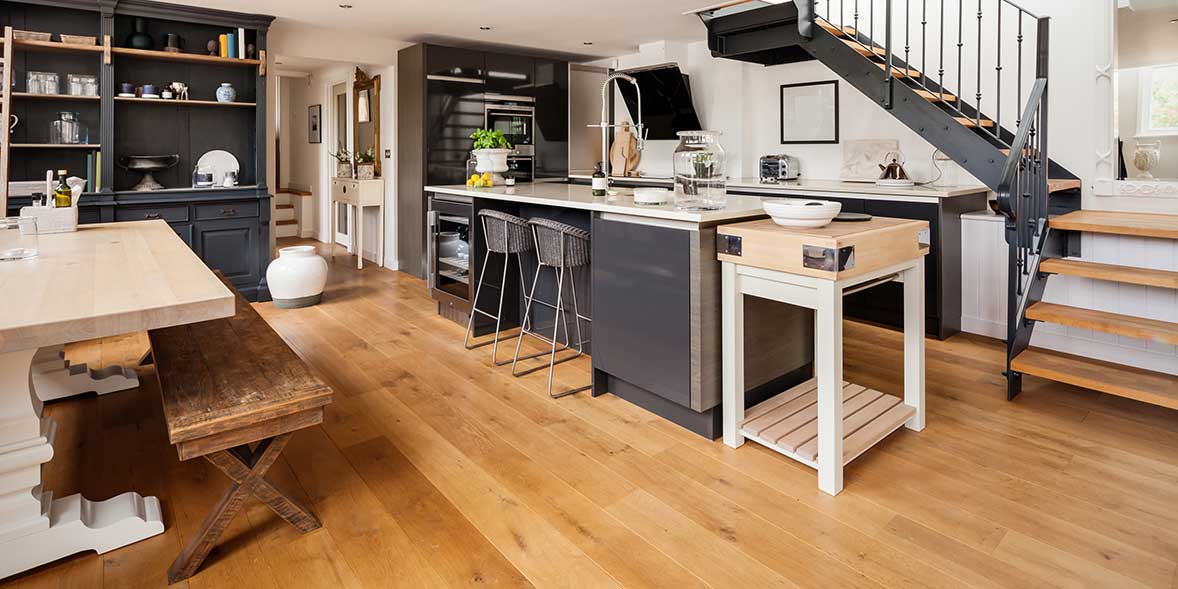
Solid wood floorboards consist of a single piece of wood, which is typically 18-20mm thick. It can be sanded back to restore the finish multiple times if it's damaged, meaning that it will last for years.
However, solid wood is very sensitive to changes in temperature and humidity. It swells in hot and humid environments, and shrinks in the cold. Over time, this can cause the floorboards to crack and warp, which will ruin the finish of your floor. And it might not be possible to use with underfloor heating – make sure you discuss this with your retailer or fitter before making a purchase.
Wood is a natural material and the planks will vary a little in colour. Think about whether you want a uniform look or a set of planks with a range of light and heavy grains.
Note that solid wood floorboards can amplify sound, so rugs are a good option if you have boards upstairs.
How much does solid wood flooring cost?
Prices vary depending on the cost of raw wood, from £15 per square metre for the cheapest options to £82 per square metre for some tropical hardwoods.
Where to lay solid wood flooring
Because solid wood is sensitive to temperature and humidity changes, it isn't normally suitable for bathrooms or kitchens.
It's best installed in living rooms, dining rooms and bedrooms.
Discover the best vacuum cleaners and best cordless vacuum cleaners to help keep your floors spotless
Parquet flooring
Pros of parquet flooring
- Durable, with a traditional look and feel
- A desirable feature for homebuyers, so it can increase your home's resale value
Cons of parquet flooring
- Expensive and difficult to install
- Sensitive to its environment – can fade in direct sunlight and be damaged by moisture
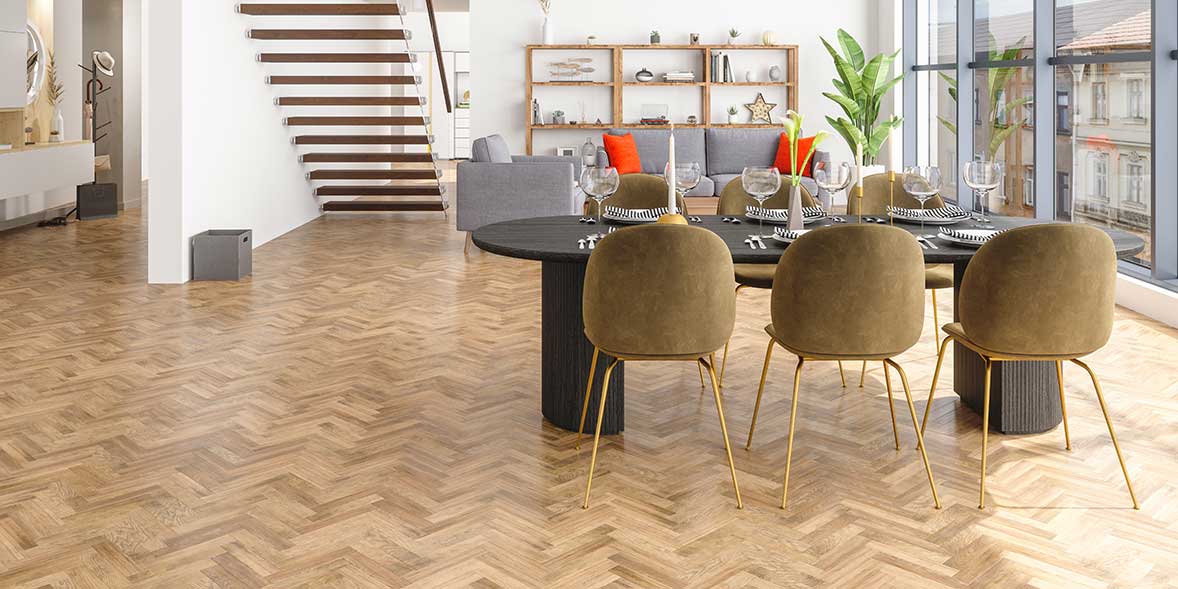
Parquet flooring is typically made of solid or engineered wood blocks arranged in a distinctive geometric pattern – usually herringbone or basket weave.
It is highly durable and can last for well over 50 years with the proper maintenance.
If you opt for parquet wood with engineered boards, you will also gain all the benefits of this type of flooring, including improved moisture resistance.
How much does parquet flooring cost?
Parquet prices start from £25 per square metre and go well into the hundreds.
Where to lay parquet flooring
Parquet flooring is suitable throughout a property, but best avoided in humid areas such as bathrooms.
If you are considering a new floor, check out our guide to underflooring heating installation and costs
Wood-effect tiles
Pros of wood-effect tiles
- Suitable in any room
- Won't rot or warp when they get wet
- Easy to maintain
Cons of wood-effect tiles
- Can be cold without underfloor heating
- Noisy to walk on
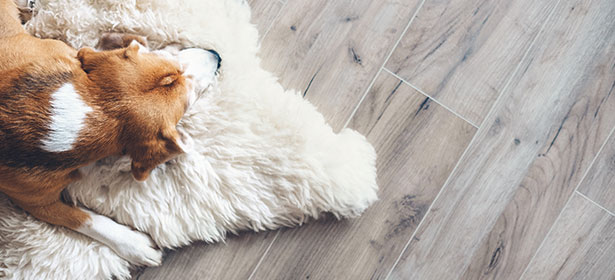
Wood-effect tiles have patterns and textures that mimic wood, but are much easier to maintain.
They offer the benefits of tiles – moisture-resistance, durability and resistances to moisture – but they can feel cold and hard underfoot.
How much do wood-effect tiles cost?
Prices vary from around £12 per square metre to more than £150 per square metre.
Where to lay wood-effect tiles
Wood-effect tiles are waterproof and much more resistant to wear and tear than hardwood and laminate floors, so they're ideal in bathrooms, kitchens and high-traffic areas such as hallways.
Some brands make matching indoor and outdoor tiles, so that you can continue your flooring from the kitchen out on to patios and porches.
Wood-effect vinyl flooring
Pros of wood-effect vinyl flooring
- Cheap
- Fairly durable (luxury vinyl is more durable than vinyl roll)
Cons of wood-effect vinyl flooring
- Hard to repair
- Doesn't last as long as solid or engineered wood
- It's made of plastic, so it won't biodegrade, and it's also incredibly energy-intensive to source and create
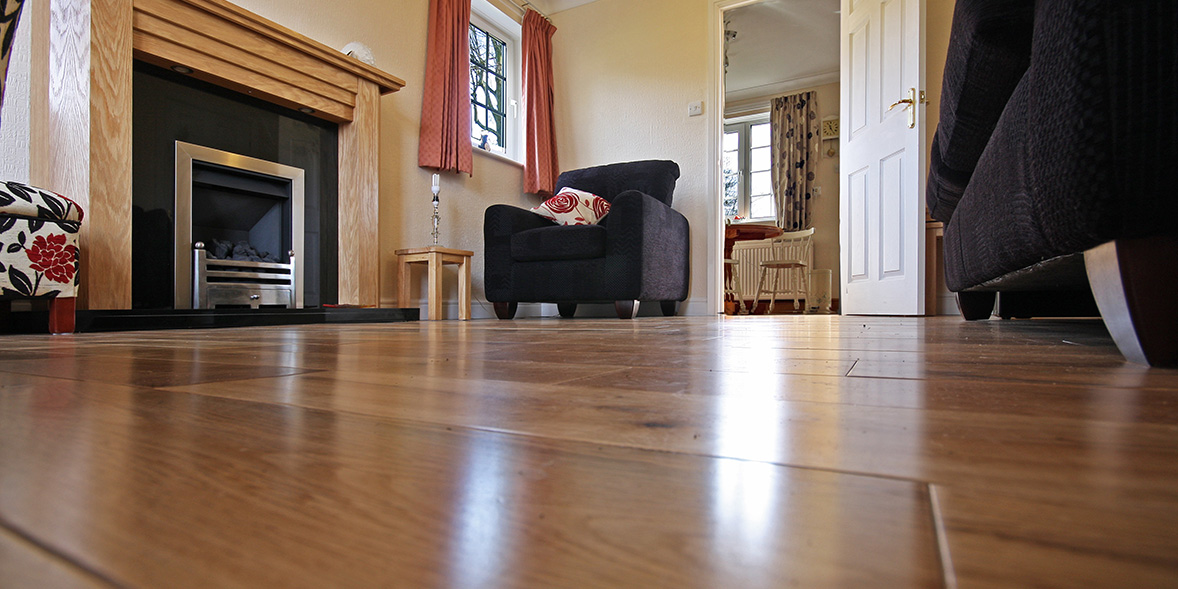
Wood-effect vinyl flooring consists of a solid vinyl sheet, topped with a printed layer in a wood-effect design and a protective overlay.
Similar to laminate, the quality can vary considerably, so it pays to buy the best quality wood-effect vinyl you can afford.
Traditional options, like vinyl roll, tend to be cheaper and less durable. However, luxury vinyl tiles (LVT) are a newer, more durable option. These come in planks and are more aesthetically appealing than traditional options.
Traditional vinyl options can also release volatile organic compounds (VOCs), which detrimentally impact air quality and health. Ensure you choose VOC-free vinyl flooring with certifications like GREENGUARD or FloorScore.
Is LVT better than engineered wood?
Luxury vinyl tiling is cheaper and more water-resistant than engineered wood, making it better suited to rooms with a lot of humidity, like bathrooms or kitchens.
However, LVT is less authentic and generally less durable, so if you're looking for an investment option for a bedroom or living room, it's worth considering engineered wood flooring.
Redoing your kitchen? See our guide to the best and worst kitchen brands
Reclaimed wood flooring
Pros of reclaimed wood flooring
- Environmentally friendly
- Can add resale value to your home
Cons of reclaimed wood flooring
- Can be expensive and difficult to source
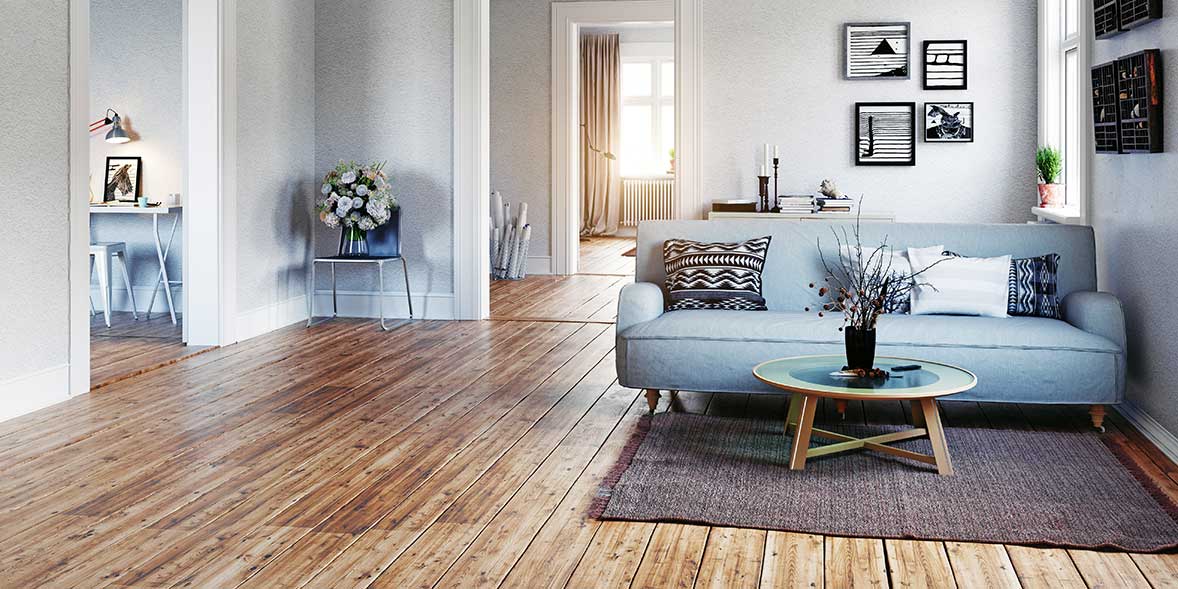
Reclaimed wood flooring is solid wood that has been salvaged for re-use from another property.
It has all the same benefits as solid wood, but is much more environmentally friendly. It will also show natural signs of wear, adding character to a room.
However, because it's labour intensive to source and remove, it can be very expensive. If cost is a factor, consider reclaimed soft wood instead. Just bear in mind that it will likely be more worn than hardwood.
How much does reclaimed wood flooring cost?
Prices vary depending on where you buy. You might find someone giving floorboards away free or cheaply on marketplace sites such as eBay and Facebook Marketplace.
At salvage yards, boards tend to start from about £25 per square metre. This can rise to well over £100 per square metre depending on the condition, age, type of wood and width of boards.
Where to lay reclaimed wood flooring
Reclaimed timber flooring can be installed anywhere, but it's best avoided in bathrooms where moisture may cause the timber to swell and crack.
Bamboo flooring
Pros of bamboo flooring
- Sustainable
- Good for those with allergies (it repels dust and pollen and is it's inhospitable to dust mites)
- Strand-woven bamboo is tougher than oak flooring
Cons of bamboo flooring
- In some bamboo flooring, the adhesive used contains formaldehyde, a toxic substance that can release small amounts of volatile organic chemicals (VOCs) over time
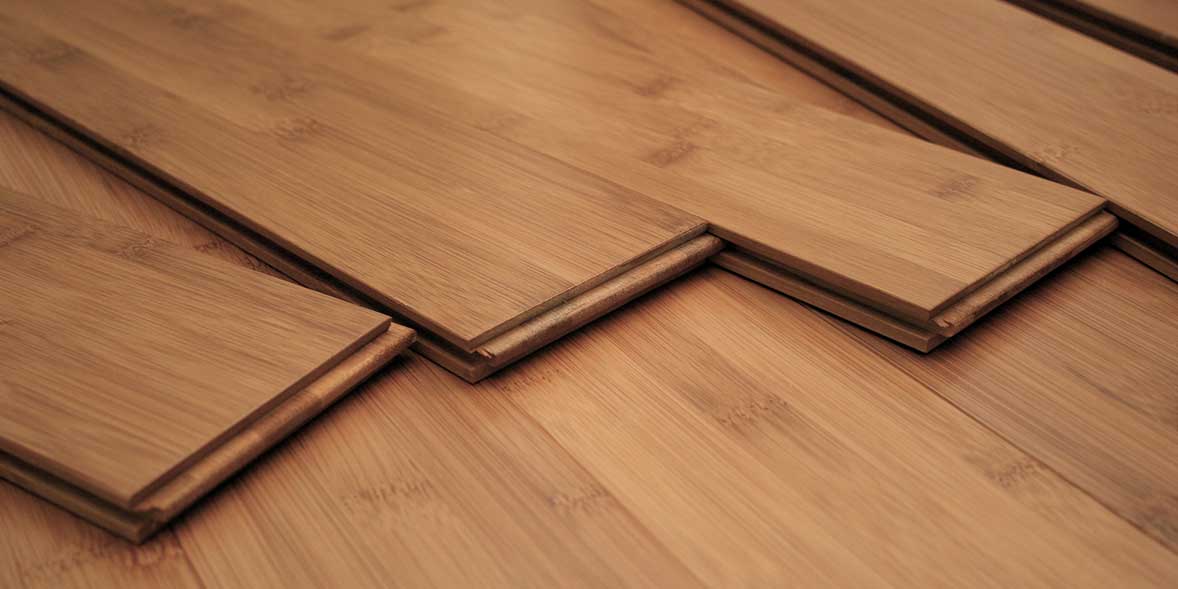
Technically a grass rather than a wood, bamboo reaches maturity in a quarter of the time of hardwood trees, which means it's more sustainable to harvest.
Bamboo forms its own unique grain pattern and can be worked into extremely hard-wearing floorboards that look and feel very similar to natural hardwood. It's also easy to clean.
The material is water resistant (so less likely to develop mould and mildew), but not waterproof – too much water can leave unsightly spots and cause the flooring to warp. Darker bamboo has been through a carbonisation process, which weakens the material and makes it softer and more prone to scratching.
How much does bamboo flooring cost?
Prices vary, but start from about £20 per square metre.
Where to lay bamboo flooring
Bamboo works well in most rooms. Although it's more water resistant than hardwood, it's not waterproof, so it's best avoided in bathrooms.
Cork flooring
Pros of cork flooring
- Sustainable
- Absorbs sound
- Keeps naturally warm all year round
- Doesn't absorb dust or mites (making it good for those with allergies), shock-absorbent and durable, so it can withstand plenty of foot traffic
Cons of cork flooring
- Unlikely to last as long as hardwood floors
- Can be scratched, making it susceptible to furniture damage
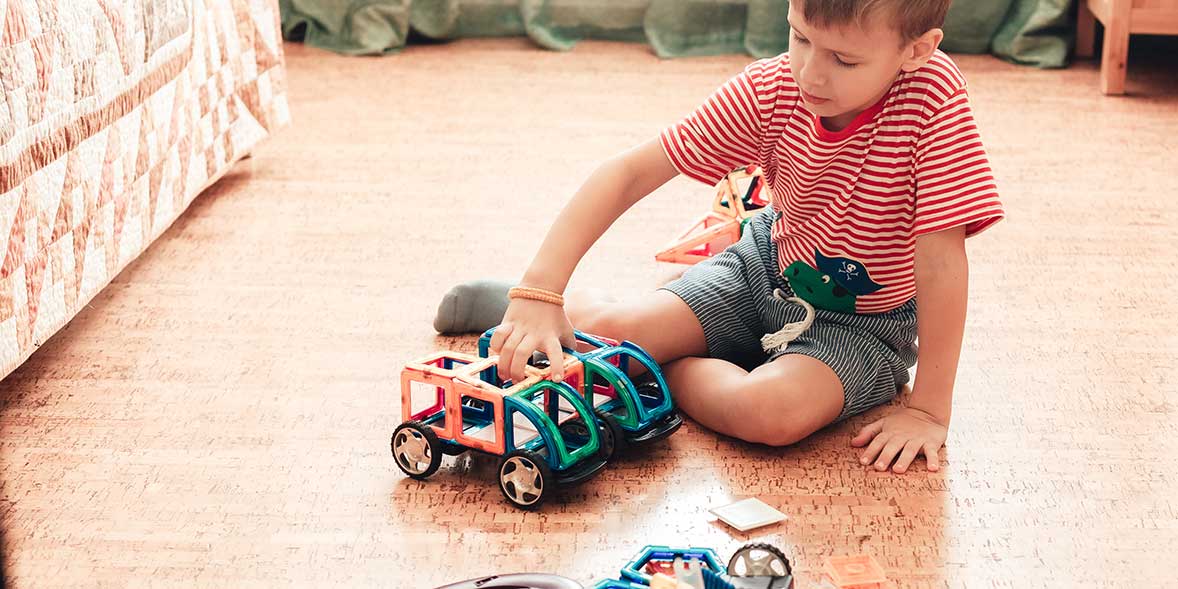
Cork is actually the bark of the cork oak tree. Bark naturally splits periodically – around every nine to 15 years – and can be safely harvested without harming the trees.
The bark regrows and the cycle continues, and it's biodegradable at the end of its life cycle, making it an eco-friendly flooring option.
For flooring, cork is ground up, compressed and formed into sheets bonded with resins.
How much does cork flooring cost?
Prices start from about £20 per square metre for cork tiles.
Where to lay cork flooring
Cork has a soft surface that can have a slight cushioning effect, so it can be a great choice for children's bedrooms or playrooms. It also retains warmth, so will feel cosy underfoot in bedrooms.
Cork floor tiles are finished with a clear varnish that gives protection against water stains and damage. However, if the seal isn't perfect and the tiles are exposed to water, they could warp and discolour. High humidity can also cause cork to curl, so it's best to avoid it in bathrooms.
Discover how to buy sustainable furniture
Tongue-and-groove vs click-lock flooring
As well as choosing the type of wood floor you want, you'll need to decide on the type of installation method.
This can have a huge impact on the durability – and price – of your floor.
Tongue-and-groove flooring
With tongue-and-groove flooring, each plank has a protruding 'tongue' along its length that fits into a 'groove' on the adjacent plank.
Fixing tongue-and-groove together can be quite complicated. Once the tongue is in the groove, you have to knock it firmly into place. If you get the angle wrong, you could dislodge planks that you’ve already joined.
They also need to be glued into position and wedged or strapped together until the glue is set. Using insufficient glue or failing to hold it tightly together before it sets can lead to gaps between planks.
Click-lock flooring
Click-lock flooring has edges that are machined to form an interlocking joint that you click together.
It’s generally considerably easier and quicker to fit a click-lock floor, as the edges don't need to be fastened with an adhesive. What’s more, the interlocking mechanism creates tight-fitting joints, reducing the chances of gaps forming after it has been fitted.
Opting for click-lock flooring means the planks can be unfastened and lifted out if you need to get access under the floor, which you can’t do with tongue-and-groove flooring.
What is the cheapest wood flooring?
If you're aiming to keep costs low as you upgrade your home, laminate flooring is worth a look – you can expect to spend around £20 to £25 per square metre. It's also widely available in many shades, so you shouldn't have trouble finding laminate flooring that suits your unique style.
Bevelled edges, a more varied set of wood-effect patterns, and embossed features like knots will give a more natural look and texture, but they cost more. Brands such as QuickStep (about £18 to £44 per square metre) and Pergo (about £18 to £49 per square metre) offer more premium options.
Where to buy wood flooring
Whether you're shopping online or in store, make sure you pay attention to the shop's returns policy.
Popular online retailers that stock wood flooring include:
- B&Q Sells both solid wood flooring and engineered wood flooring. Engineered boards are the cheaper of the two, with prices starting at around £14 per square metre.
- Tapi has laminate, vinyl and luxury vinyl flooring starting from around £20 per square metre. They also stock an embossed vinyl floor that mimics the texture of real wood.
- Pergo The brand offers laminate, vinyl and wood flooring and you can filter to pick out a water-resistant option suitable for bathrooms.
- Quick-Step Offers hardwood flooring starting at around £63 per square metre. Vinyl is more affordable, starting at around £38 per square metre.
- UK Flooring Direct Affordable laminate flooring starting at around £12 per square metre for a steel grey finish.
Find out which retailers are rated highly by Which? members with our expert guide to the best stores for DIY, decorating and furniture